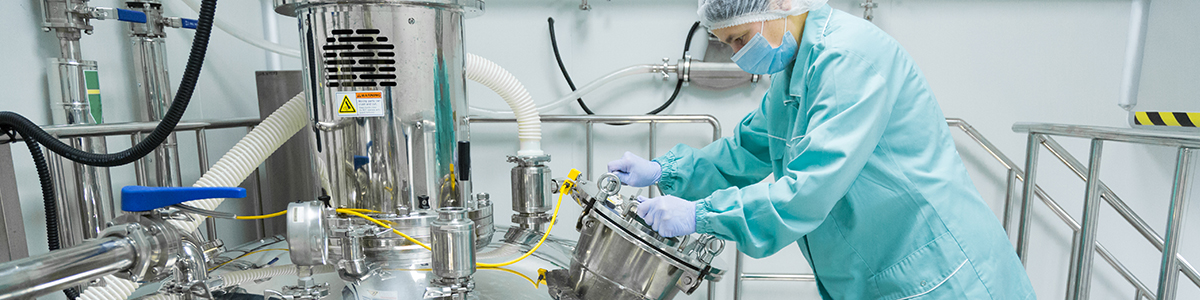
Process Safety and Risk Management are fundamental to mitigating hazards and ensuring the integrity of small molecule development, from early-stage discovery through to commercial-scale manufacturing. At Aragen, we prioritize these principles across every stage of the development lifecycle.
We work closely with our clients to ensure that each phase—from early-stage feasibility studies to full-scale commercial manufacturing—is executed with a focus on safety, scalability, and regulatory compliance. Our comprehensive approach includes advanced screening tools, risk assessments, and a deep understanding of safety regulations, which enables us to identify, assess, and mitigate potential risks at every stage.
With a commitment to safety and reliability, our experienced team helps facilitate a seamless transition from early-phase research to large-scale production, empowering clients to bring their small molecules to market faster, safer, and with confidence.
Process Safety: Methodology for assessing NCE development
Laying the Foundation for Safe and Feasible Manufacturing
In the early phase of drug development, the primary focus is on evaluating potential risks and setting up a safe, feasible synthetic route for the New Chemical Entity (NCE). As your CRDMO partner, we ensure that Process Safety is a core consideration, starting from the initial stages of feasibility.
Approach
Risk Management Focus
Informed Process Design: By proactively addressing potential risks, we guide our clients in choosing the best route to scale-up and commercialize their small molecule.
Advanced Risk Management for Scale-Up and Formulation
As the project progresses into the late phase, our risk management strategies become more advanced. We focus on ensuring that the synthesis, scale-up, and formulation processes are free from safety hazards and scalable for commercial manufacturing.
Approach
Risk Management Focus
Ensuring Scalable, Safe, and Compliant Manufacturing
As the process moves into the commercial phase, ensuring that your small molecule production is safe, compliant, and scalable becomes our top priority. We perform thorough safety evaluations and risk management assessments, ensuring that your process meets regulatory requirements while maintaining high standards of safety.
Approach
Risk Management Focus
Process Safety Laboratory – Infrastructure
Aragen provides end-to-end CMC support for IND applications, ensuring quality, compliance, and success through integrated process chemistry, manufacturing, and analytics.
Ensures seamless drug substance technology transfer across all phases, mitigating technical, regulatory, and quality risks for successful commercial-scale production.
Aragen reliably develops and manufactures high-potency APIs, including cytotoxics, drug linkers, PEG conjugations, and ADC toxins, ensuring safe, effective solutions.