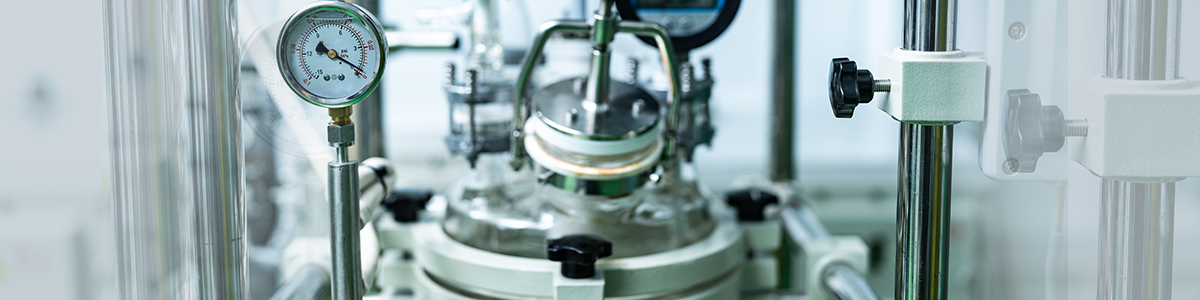
Late-stage development is a critical phase for optimizing and scaling up the manufacturing process of small molecules, ensuring that the drug substance can be efficiently produced at a commercial scale. At Aragen, our Process Development & Optimization services are designed to ensure that your small molecule is developed efficiently, with a focus on improving yield, repeatability, minimizing costs, and enhancing product quality. We follow RFT (Right First Time) approach by using Quality by Design principle during process development. Our team work closely with you to refine each step of the process, from the initial synthesis to final manufacturing, to ensure your product is ready for the complexities of large-scale production.
By leveraging advanced technologies like DoE, BlazeMetrics, Flow chemistry, rigorous testing, and a deep understanding of pharmaceutical manufacturing, we help you achieve a seamless transition from clinical phases to commercial-scale production. Our expertise ensures that your process is not only scalable but also optimized to meet the growing demands of the market while maintaining product quality and regulatory compliance.
Process Development & Optimization Services
We specialize in refining and enhancing processes that are already in development, focusing on safety, optimizing yield, purity, and efficiency as you transition from clinical phases to continuous large-scale manufacturing.
Comprehensive Process Analysis
Our experts follow DMAIC methodology in all the process development activities. Our experts continuously interact with your team to understand the process in detail and identify the problem statement (potential inefficiencies, bottlenecks) to finalise the objective for the study. We use advanced modelling and simulation tools, in-line PAT (Process Analytical Technology) tools to track the process and predict how small changes might affect large-scale production allowing us to proactively address issues before they arise. This process includes:
Process Improvement/ Refinement
Our process improvement/refinement services focus on optimizing key aspects of the manufacturing process to improve yield, purity, efficiency, and scalability while minimizing costs and environmental impact. To achieve them, our experts follow scientific and data-driven approaches including:
Scale-Up Services
Successful scale-up is critical for moving a small molecule from the lab to large-scale commercial production. We are experts in managing the challenges of scaling, from volume increase to process consistency, while ensuring product quality and regulatory compliance are maintained at every step. Our scale-up services ensure that your production process maintains consistency and efficiency at every stage.
Lab-to-Pilot and Commercial-Scale Transition
Our team excels at translating lab-scale processes to pilot- and commercial-scale production, maintaining the integrity and performance of your small molecule throughout. We manage this process through:
Production Volume Management & Capacity Optimization
Scaling a process goes beyond expanding batch size and is about ensuring consistent quality and reliability across all stages of production. Our scale-up services include:
Minimization of Impurities and Variations During Scale-Up
One of the most critical challenges during scale-up is minimizing process variability and ensuring consistent product quality. Our approach includes:
Advanced Reactor Systems for Large-Scale Production
Our Scale-Up Lab is equipped with a range of state-of-the-art reactors and equipment designed to handle the increased volume and complexity of late-phase drug substance production. We offer reactors from 60L to 630L and utilize a variety of associated utilities to optimize your manufacturing process.
Additionally, our facility is equipped with a range of advanced systems designed to handle a variety of reaction conditions and production scales, from small-scale synthesis to kilogram-scale manufacturing. These include: