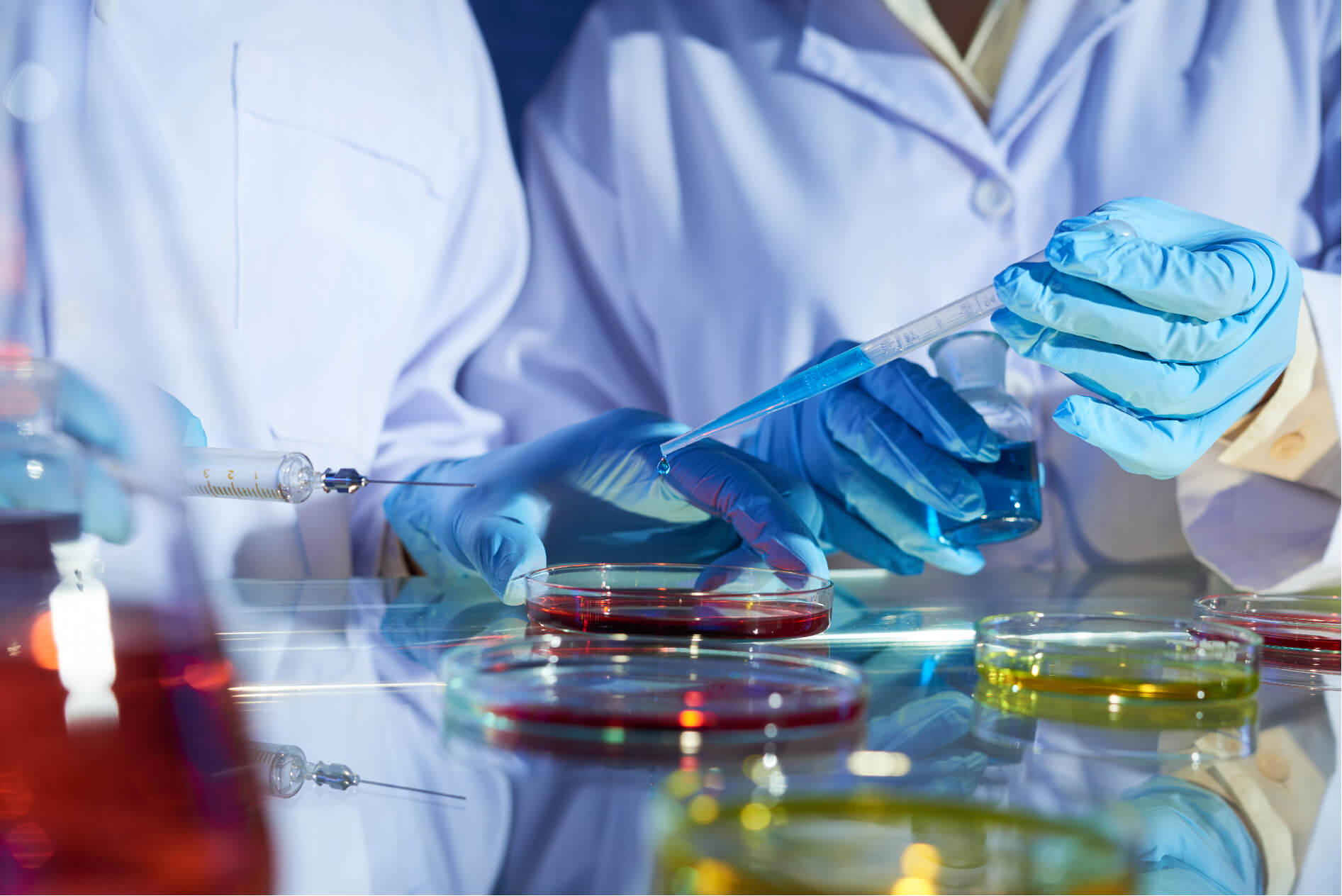
The client was screening a specific Monoclonal Antibody (mAb) against a species of bacteria that causes several difficult-to-treat infections such as pneumonia and cystic fibrosis lung infection. This mAb candidate was being developed as a first-in-class adjunctive therapy. Aragen was approached to identify the high producing clone and to develop an upstream process development protocol for achieving greater therapeutic titers at different bioreactor levels, streamlining GMP manufacturing.
The client is a late-stage clinical development company leading the creation of transformative, first-in-class anti-infectives for life-threatening viral and bacterial respiratory infections. The company’s pipeline of novel mechanism antibacterial and antivirals, sprung from its proprietary technology platforms, are designed to combat the growing public health threat of viral pandemics and antimicrobial resistant (AMR) bacteria.
A multipronged approach was adopted to identify the high producing clone among the three developed by the client and to establish the optimum experimental parameters for upstream process development both at shaker flask and bioreactor levels. The cell line development team worked closely with the client’s technical team for the tech transfer. Aragen’s bioprocess technologists validated the optimum parameters at bench and pilot scale and all the analytics was performed by the developability team ensuring an unfailing and scalable upstream process. The process was developed in accordance with appropriate standards and was in accordance with industry best practices. All the complications and the associated risks in the developed process were consistently sought out and rectified to ensure the quality certified process to the client.
The process development began with tech-transfer of three RCB clones from the client’s laboratory to Aragen’s. To identify the superior clone first step was to increase the quantity of all the three clones i.e., to generate the development cell banks (DCBs). Initial shaker flask studies were conducted with all three DCBs using media, feed, and experimental conditions like those of the client and based on metrics such as protein titer and other physicochemical characteristics one clone was selected for master cell bank (MCB) development. Media and feed screening were performed on the selected clone using a shaker flask, and eight different media were tested.
After extensive DOE in shaker flask, screen assessment, and parameter optimization, the process was translated to pilot scale bioreactors (2L). Paraments were further optimized in pilot scale and the product was analyzed for its physicochemical characters using high throughput analytical techniques. Optimised parameters were tested for scalability in 7L bioreactor and finally the optimised upstream process was transferred to client’s preferred CDMO. The total increase in the titer after the bioreactor evaluation was equivalent to 116% with titer improving at every stage of the process development.
Step 1: Technology transfer
Step 2: Feed screening and selection of a clone
Step 3 – Media and feed screening for the selected clone
Step 4 – Process parameter and screen evaluation in 2L and 5L bioreactor
The total increase in the titer of the harvest was equivalent to 116% with titer improving at every step of the process development. The efficient process development developed by Aragen was submitted to the client for scaling up to GMP manufacturing. Subsequently, the client successfully conducted Phase I trials.